The time has come to finally start a new build. I thought that my single seat buggy was next on the list since it was already on the chassis table, but having a son changed my priorities. I picked up a farm fresh 1969 Commando for a pretty good price, or so I thought. It turns out that it is a little more rotten than I expected after my initial inspection.
This is a two owner 1969 Jeepster Commando built by the Kaiser company. It has the original 231 V6, automatic transmission, and dana 20 transfer case. I was told the motor got a knock in it back in 91 right as the owner was getting ready to leave for college. He parked it out in the field and bought something more reliable. 24 years later it was drug out of the field and to my shop. Apparently he thought he was a pretty good mechanic because this thing is pretty much butchered. There was an additional heater box installed and ducked to the back. I am sure that it helped, but it was cobbled in and plumbed with PVC. The hardtop clearly became friends with a tree at some point. The hardtop seems pretty roached so it might not make it back.
The original plan was to pop out the drivetrain and upgrade it to a 4.0L, ax15, NP231 and dana 44s. Toss some 33's on it and a cage. Once I realized what shape it was in and how much work I was looking at I turned this ship onto a new course.
The current plan is a full custom box tubing frame. Four link and coilover the front, leaf springs in the rear. 4.0l, ax15, and a dana 300. Then custom tube fenders front and rear, a full family friendly cage, soft top, fix the roached metal, and armor the crap out of it. Toss on a set of 35" km2s and go wheel it.
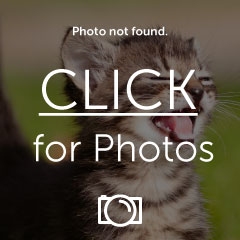
This is a two owner 1969 Jeepster Commando built by the Kaiser company. It has the original 231 V6, automatic transmission, and dana 20 transfer case. I was told the motor got a knock in it back in 91 right as the owner was getting ready to leave for college. He parked it out in the field and bought something more reliable. 24 years later it was drug out of the field and to my shop. Apparently he thought he was a pretty good mechanic because this thing is pretty much butchered. There was an additional heater box installed and ducked to the back. I am sure that it helped, but it was cobbled in and plumbed with PVC. The hardtop clearly became friends with a tree at some point. The hardtop seems pretty roached so it might not make it back.
The original plan was to pop out the drivetrain and upgrade it to a 4.0L, ax15, NP231 and dana 44s. Toss some 33's on it and a cage. Once I realized what shape it was in and how much work I was looking at I turned this ship onto a new course.
The current plan is a full custom box tubing frame. Four link and coilover the front, leaf springs in the rear. 4.0l, ax15, and a dana 300. Then custom tube fenders front and rear, a full family friendly cage, soft top, fix the roached metal, and armor the crap out of it. Toss on a set of 35" km2s and go wheel it.